Dry Wash Technology
- 27 Apr 2010 1:00 AM
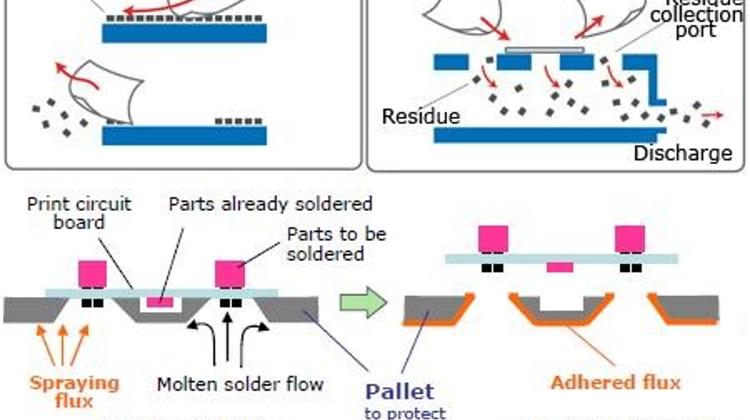
The dry washing technology is based on the principle of using airflow to blast thin resin films onto the object to be cleaned and removing the residue with their impact or contact. The thin and lightweight film, which does not damage the object to be cleaned, effectively removes residue at the edges that cannot be removed by high-speed airflow alone.
This process uses neither solvent nor water, and it also minimizes the amount of material used for the thin and lightweight film. Its capacity for removing residue does not diminish after repeated use, so the resin films can be used continuously without being replaced. Only residue removed from the object is discharged, with the resin films used repeatedly through continuous circulation. These properties make it possible to reduce both environmental impact and operational cost.
Ricoh has been researching and developing dry washing technology that eliminates waste liquid in order to recycle the products, such as copiers or printers. Ricoh has applied this technology to the washing of pallets used in the automated soldering process. Although pallets are generally cleaned with solvents, we have achieved solvent-free washing with this technology.
Jigs called pallets are used in the automated soldering process to protect already-soldered parts from heat. In this soldering process, liquid flux is applied to eliminate the oxidized layer of the joining surface, but the flux gets laminated and adheres to pallets through repetitive use. The flux remaining on pallets must be cleaned off periodically.
Solvent cleaner is commonly used to remove the adhered flux, which places a burden on the environment and incurs disposal costs for the waste liquid. Also, in terms of safety and health, a solvent-free washing method is desirable.
Ricoh has been further developing dry washing technology, which was originally developed to remove toner from parts or components, and, while doing so, the company found a way to remove even adhered flux without using solvent cleaner.
Pieces of film can be easily separated from the removed residue (flux powder) because of the difference in the sizes between the film and the flux powder. Only the flux powder is collected by a dust collector and the films are used repeatedly through continuous circulation.
This new method can reduce both environmental impact and washing costs by up to one tenth compared with the conventional method using solvent. Washing time has also reduced from more than 2 hours to less than 5 minutes.
Water has been used in the conventional washing process to reclaim parts and components covered with toner. This process requires time and energy for dewatering and drying, and moreover, wastewater generates an environmental impact and processing costs.
Ricoh has developed dry washing technology that does not require dewatering and drying. As a result, a process that used to take more than 1 hour has been shortened to about 1 minute, and wastewater has been reduced by 2.4 tons per month."
Source: ricoh.hu
LATEST NEWS IN business